Textile Printing Process Flow Chart
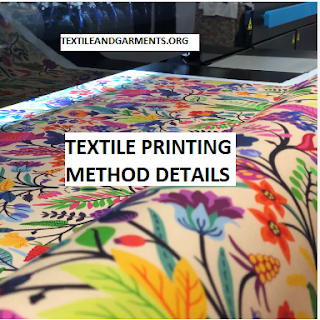
Textile Printing Process Flow Chart Introduction Textile Printing involves localised colouration. This is usually achieved by applying thickened pastes containing dyes or pigments onto a fabric surface according to a given colour design. In particular, the viscosity of a print paste is critical. It determines the volume of paste transferred to the fabric and the degree to which it spreads on and into the surface yarns. The paste must colour all the visible fibres on the printed surface, so it must penetrate somewhat into the yarn structure. If the paste is too 'thin', it will spread, giving poor print definition, and penetrate too far into the yarns decreasing the colour yield. Printing was originally done by hand using wooden blocks with a raised printing surface, much as children do potato printing. The two main techniques used for transferring paste onto fabrics involve engraved rollers carrying paste in the recesses corresponding to the colour pattern, or screens with the...